Gerd Schwaderer
Volume Graphics GmbH
Gerd Schwaderer
- History: Imageware
- American startup (50+)
- Application engineer, then sales
- First ones to handle pointclouds
- Reverse Engineering, little inspection
- Automotive & Aerospace
- Best partner of GOM, sharing resellers
- Aquired 2000 by SDRC for 30mio€
- History: 2000-2001, SDRC Ford Program Office
- American CAD company (1000+)
- Supplier of Fords CAD solution
- European Application Specialist
- Ford Design Center
- Reverse Engineering, Inspection & Power Wall
- SDRC aquired 2002 by EDS
- History: 2001-2002, EDS Automotive Specialist
- American IT company (100.000+)
- Largest IT company besides Intel
- Acquired Unigraphics & SDRC
- Today this department is Siemens NX
- European Application Specialist
- Ford Design Center
- Reverse Engineering, Inspection & Power Wall
- Left EDS before it brought Unigraphics to the stock market
- History: 2003-2013, Geomagic Sales Manager
- Sales Manager EMEA
- Staff up to 14, up to 7.5mio/€
- Training and Maintenance responsibility
- Channel: direct & OEMs: GOM, Faro, Hexagon
- Breuckmann (Aicon), Steinbichler, KonicaMinolta, ect.
- Hundreds of Demos, even with terrestrial scanners (Iqvolution/Faro)
- Continuous fight against Polyworks
- Reverse Engineering
- Inspection
- Voxel Modelling (Freeform, acquisition in 2008)
- Plugin for Solidworks
- Custom development for medical applications (dental & hearing aids)
- Acquired 2016 by 3dSystems for 40mio$ (1000+)
- History: 2013-2016, 3DSystems
- Largest 3DPrinting company in 2016 (1000+ people)
- Acquired Geomagic for 40mio$
- Moved in Business Development Role
- CAD Software: Alibre
- Voxel Modelling: Freeform
- Not: Cimatron (CAM): Part of 3DS
- Left 3DS in 2016 to Volume Graphics
- History: 2016 – today vision: Volume Graphics
- Make inspection obsolete
- At least the 2D drawings
- Virtual Metrology on simulation
- DOE, Design of experiments
- Make production more sustainable
- Make it easier
- Use like CAD, smart inspection
- Integrated
- PMI
- Better communication & visualisation
- Multi part handling
- Make it complete
- Few GD&T functions missing
- Supply help instead of raising red flag
- In advance or once it happened
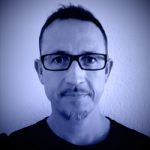
When Metrologists start to talk with Simulation
Generative design, lights out production and automated inspection are state of the art and work. What can the user do to optimize the process, minimize iteration cycles and create, as wanted in additive or plastic injection molding, a “first product right”? That’s quite a lot, which is due to the complex production process with the many parameters involved, material challenges and different behavior for every shape, dependencies even printer or location of the product on the print bed. Certainly we have to admit that the whole inspection industry only exists because things go wrong, but we also have tools to minimize the scrap, iterations and waste. One major application is using simulation, metrology on simulated parts, AI based processing of the results and compensation by morphing geometry. Its almost a complete virtual workflow to enable the producer to simulate the whole production process of additive or molding and take care before wasting considerable time, money, energy and materials. In short: Simulate the print process, measure the result, feed back the information to Dfam or Design, compensate by changing parameters, supports, layout or compensate the initial shape by morphing it. Even the metrology part may need morphing to enable quicker metrology results by bending the initial measurement template onto the actual, deformed scan. It may even start with simulating CT scans of the designed product to figure out, if the design is cooperative in an industrial CT and lets the producer inspect it, providing the proof of inspectability in time.