B. Ahmed Chekh
Tekniker
Ahmed Chekh
Ahmed Chekh is a mechanical engineer who received his Master’s degree from the University of the Basque Country. Currently, he works as a researcher in the precision engineering research group at Tekniker, a technological center located in the Basque Country, Spain. His research focuses on the development of measurement equipment, systems, and procedures for new metrology industrial solutions. He has participated in various European, national, and local projects related to precision engineering and metrology.
As a researcher, Ahmed Chekh, has expertise in the areas of robotics, machine tools, and measurement technologies, such as photogrammetry and Laser Tracker. Specifically, he specializes in the modeling of measurement systems and calibration procedures, where he has a strong know-how in creating simulation tools to estimate the uncertainty of different measurement systems and procedures.
He has just started his PhD in mechanical engineering, where he aims to develop accurate and reliable digital twins for complex production means, including industrial robots and machine tools, as well as measurement technologies.
In the field of research, he has published several papers in international journals and presented his work at various conferences and workshops.
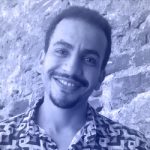
Development of software application for the off-line robot program compensation in 6 DoF (RoboKom)
The presented work focuses on the development of a software application called RoboKom, which is aimed at compensating the robot program in 6 degrees of freedom. The methodology used involves modelling the robot using kinematic and elastic parameters and calibrating these parameters using various robot calibration methods. The calibrated parameters are then implemented by offline correction of the robot programs. The results show that the robot program can be compensated in 6 DoF, achieving positional accuracy on the order of robot repeatability (30 μm). The main advantage of this approach is the capability to implement the calibrated robot parameters through off-line program correction, which is limited for most robot manufacturers. Additionally, program-based compensations are presented where robot modelling is not required.