Pablo Antunes da Rosa
Boticario Group
Pablo Antunes da Rosa
Pablo Antunes da Rosa is Brazilian, holds a degree in Mechanical Engineering from the University of Caxias do Sul, with a sandwich period at Technische Universistät Ilmenau (Germany) and a Master’s degree in Mechanical Engineering with emphasis on Metrology and Instrumentation from the Federal University of Santa Catarina when he developed a methodology of dimensional evaluation of flexible parts without the need for fixation used by the Brazilian aeronautical industry. He is currently a PhD candidate in Mechanical Engineering at the Federal Technological University of Paraná and works as a Metrology Specialist at the Materials Technology laboratory of Grupo Boticario (a company in the field of personal hygiene products, perfumery and cosmetics) developing validation methodologies for packaging and accessories. In 2020, Pablo received the Zeiss Measuring Hero award and has been working to develop new possibilities for dimensional control of products.
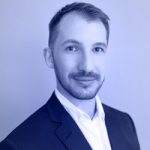
Metrological evaluation of 3D printed Poly(Lactic Acid) fixtures by Fused Deposition Modeling (FDM
The cosmetics, hygiene and perfumery industries are characterized by the dynamicity of their portfolio associated with their large number of products. This aspect makes the quality control of the dimensional attributes challenging when evaluated in Coordinate Measuring Machines (CMM), for example, since it is necessary to use specific fixtures to guarantee the repeatability of the positioning during the test. In this way, this project sought a way to reduce the costs and time of design/manufacture of fixtures by the conventional method (machining) with additive manufacturing, also allowing its geometric optimization. In this study, a fixture was computationally modeled and then manufactured through the process of Fused Deposition Modeling (FDM) with poly(lactic acid)(PLA) filament with three different printing densities (D1, D2 and D3) and associated with spheres of steel resulting in a 3-2-1 fixation system, guaranteeing the immobility of the six degrees of freedom of the measurand. During the beginning of the evaluation process, the fixtures were digitized with a three-dimensional scanner (Zeiss Comet L3D 250) to monitor their geometry and subsequently underwent a thousand cycles of dimensional evaluation (CMM Zeiss O-Inspect 322) with the repositioning of the product with each measurement. The results were evaluated through a long-term stability study, after the approval of the measurement system in a repeatability and reproducibility (R&R) study and the calibration of the measurand. Furthermore, after completion of the assessments, the capability of the measurement system was expressed numerically by indices of bilateral capability (Cg) and capability for non-centralized measurement processes (Cgk) for comparative purposes. The three evaluated fixtures showed good long-term stability when compared with the tolerance of the measurand. Also, despite the difference identified in the evaluation of the process capacity, only the device with the highest density presented indexes above 1.33, thus being the only one considered capable. The comparison with the original geometry allowed identifying the contact points with the greatest variation and reflected the capacity results. This project made it possible to evaluate the application of fixtures with less design/manufacturing time, in addition to lower cost and greater ease of handling and storage. However, the balance between cost and service life compared to devices built through machining is necessary for large-scale application and in other fields of application.
The following topics will be covered in the presentation: Validation of measuring instruments and calibration of the measurand, 3D printing, Measurements and Analysis.